Research
Motion Planning for Object Manipulation by Edge-Rolling
A common way to manipulate heavy objects is to maintain at least one point of the object in contact with the environment during the manipulation. When the object has a cylindrical shape or, in general, a curved edge, not only sliding and pivoting motions but also rolling the object along the edge can effectively satisfy this condition. Edge-rolling offers several advantages in terms of efficiency and maneuverability. This paper aims to develop a novel approach for approximating the prehensile edge-rolling motion on any path by a sequence of constant screw displacements, leveraging the principles of screw theory. Based on this approach, we proposed an algorithmic method for task-space-based path generation of object manipulation between two given configurations using a sequence of rolling and pivoting motions. The method is based on an optimization algorithm that takes into account the joint limitations of the robot. To validate our approach, we conducted experiments to manipulate a cylinder along linear and curved paths using the Franka Emika Panda manipulator.
Collaborators: Maede Boroji, Vahid Danesh
![]() | ![]() | ![]() |
Publication:
- M. Boroji, V. Danesh, I. Kao, A. Fakhari, “Motion Planning for Object Manipulation by Edge-Rolling,” 2024 IEEE/RSJ International Conference on Intelligent Robots and Systems (IROS), 2024.
Development of a Novel Impedance-Controlled Quasi-Direct-Drive Robot Hand
Most robotic hands and grippers rely on actuators with large gearboxes and force sensors for controlling gripping force. However, this might not be ideal for tasks which require the robot to interact with an unstructured and/or unknown environment. We proposed a novel quasi-direct-drive (QDD) two-fingered robotic hand with variable impedance control in the joint space and Cartesian space. Variable impedance control allows the hand to perform dexterous manipulation tasks while being safe during human-robot interaction. The quasi-direct-drive actuators enable the fingers to handle contact with unstructured environment without the need for complicated tactile or force sensors. The hand demonstrates grasping with force-closure and form-closure, stable grasps in response to disturbances, tasks exploiting contact with the environment, simple in-hand manipulation, and a light touch for handling fragile objects.
MS Student: Jay Best
![]() | ![]() | ![]() |
![]() | ![]() | ![]() |
![]() | ![]() | ![]() |
Thesis:
- Jay Best, “Development of a Novel Impedance-Controlled Quasi-Direct-Drive Robot Hand,” Department of Mechanical Engineering, Stony Brook University, 2023.
Publication:
- J. Best and A. Fakhari, “Development of a Novel Impedance-Controlled Quasi-Direct-Drive Robotic Hand,” arXiv, 2024.
Motion and Force Planning for Manipulating Objects by Pivoting
Manipulation of objects by exploiting their contact with the environment can enhance both the dexterity and payload capability of robotic manipulators. A common way to manipulate heavy objects beyond the payload capability of a robot is to use a sequence of pivoting motions, wherein, an object is moved while some contact points between the object and a support surface are kept fixed. In this research, we developed an algorithmic approach for automated plan generation for object manipulation with a sequence of pivoting motions. A plan for manipulating a heavy object consists of a sequence of joint angles of the manipulator, the corresponding object poses, as well as the joint torques required to move the object. The constraint of maintaining object contact with the ground during manipulation results in nonlinear constraints in the configuration space of the robot, which is challenging for motion planning algorithms. Exploiting the fact that pivoting motion corresponds to movements in a subgroup of the group of rigid body motions, SE(3), we presented a novel task-space based planning approach for computing a motion plan for both the manipulator and the object while satisfying contact constraints.
Collaborators: Dr. Nilanjan Chakraborty, Aditya Patankar
![]() | ![]() | ![]() |
![]() | ![]() |
Publications:
- A. Fakhari, A. Patankar and N. Chakraborty, “Motion and Force Planning for Manipulating Heavy Objects by Pivoting,” 2021 IEEE/RSJ International Conference on Intelligent Robots and Systems (IROS), 2021, pp. 9393-9400, doi: 10.1109/IROS51168.2021.9636103.
- A. Patankar, A. Fakhari and N. Chakraborty, “Hand-Object Contact Force Synthesis for Manipulating Objects by Exploiting Environment,” 2020 IEEE/RSJ International Conference on Intelligent Robots and Systems (IROS), 2020, pp. 9182-9189, doi: 10.1109/IROS45743.2020.9341316.
Computing a Task-Dependent Grasp Metric Using Second-Order Cone Programs
Evaluating a grasp generated by a set of hand-object contact locations is a key component of many grasp planning algorithms. In this research, we presented a novel second-order cone program (SOCP) based optimization formulation for evaluating a grasps’ ability to apply wrenches to generate a linear motion along a given direction and/or an angular motion about the given direction. Our quality measure can be computed efficiently since the SOCP is a convex optimization problem, which can be solved optimally with interior point methods. A key feature of our approach is that we can consider the effect of contact wrenches from any contact of the object with the environment. This is different from the extant literature where only the effect of finger-object contacts is considered. Exploiting the environmental contact is useful in many manipulation scenarios either to enhance the dexterity of simple hands or improve the payload capability of the manipulator. In contrast to most existing approaches, our approach also takes into account the practical constraint that the maximum contact force that can be applied at a finger-object contact can be different for each contact. We can also include the effect of external forces like gravity, as well as the joint torque constraints of the fingers/manipulators. Furthermore, for a given motion path as a constant screw motion or a sequence of constant screw motions, we can discretize the path and compute a global grasp metric to accomplish the whole task with a chosen set of finger-object contact locations.
Collaborators: Dr. Nilanjan Chakraborty, Aditya Patankar
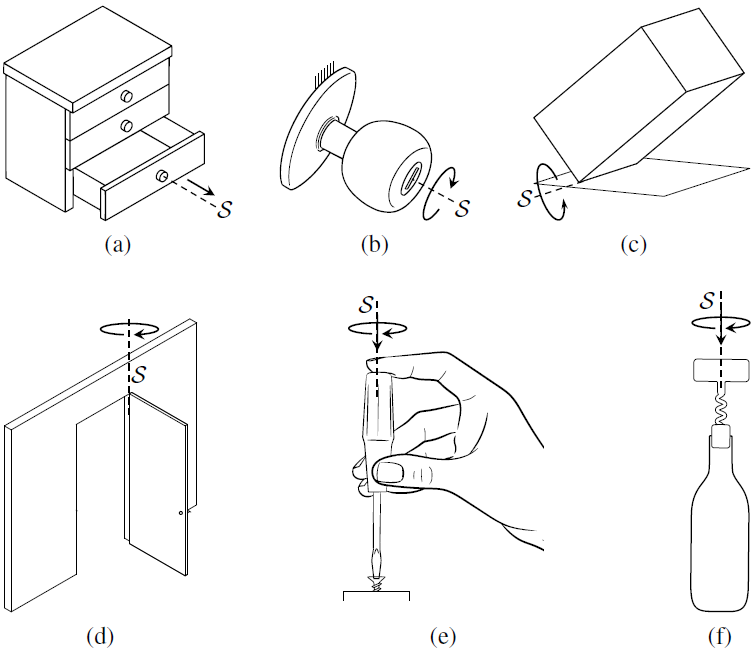
Publication:
- A. Fakhari, A. Patankar, J. Xie and N. Chakraborty, “Computing a Task-Dependent Grasp Metric Using Second-Order Cone Programs,” 2021 IEEE/RSJ International Conference on Intelligent Robots and Systems (IROS), 2021, pp. 4009-4016, doi: 10.1109/IROS51168.2021.9636197.
Development of Realistic Pressure Distribution and FLS for Soft-Finger Contact Interface of Robotic Hands
Various models have been presented for pressure distribution in the contact interface of a soft finger and object in the literature. These models have been proposed without considering the effect of the tangential forces which are usually exerted in the contact interface of a soft finger and object during grasping and manipulation. Having an accurate pressure distribution model across the contact interface is important for designing tactile sensors and improving the modeling of the friction limit surface (FLS). In this project, a new and more accurate model was proposed to describe the asymmetry of the pressure distribution in the contact interface of a hemispherical soft finger under both normal and tangential forces. According to the proposed pressure distribution model in this study, an improved and more accurate FLS was presented. This new model can provide a more accurate tool for the analysis of grasping and manipulation involving soft contact interface.
Collaborators: Dr. Imin Kao, Dr. Mehdi Keshmiri
Publication:
- A. Fakhari, M. Keshmiri, and I. Kao, “Development of Realistic Pressure Distribution and Friction Limit Surface for Soft-Finger Contact Interface of Robotic Hands,” Journal of Intelligent and Robotic Systems, vol. 82, iss. 1, pp. 39-50, 2016.
Dynamic Modeling and Control of Planar Slippage in Object Grasping and Manipulation Using Robotic Soft Fingers
Slippage occurrence has an important role in stable and robust object grasping and manipulation. However, in the majority of prior research on soft finger manipulation, the presence of the slippage between fingers and objects has been ignored. In this research, a general method for dynamic modeling of planar slippage was presented. In this method, different states of planar contact were replaced with a second-order differential equation. This kind of formulation of the system dynamics facilitates the design of model-based controllers to cancel the undesired slippage that occurs between the soft tip and object during the manipulation.
Collaborators: Dr. Imin Kao, Dr. Mehdi Keshmiri
Publications:
- A. Fakhari, I. Kao, and M. Keshmiri, “Modeling and Control of Planar Slippage in Object Manipulation Using Robotic Soft Fingers,” ROBOMECH Journal, vol. 6, iss. 15, 2019.
- A. Fakhari, M. Keshmiri, I. Kao, and S. Hadian Jazi, “Slippage Control in Soft Finger Grasping and Manipulation,” Advanced Robotics, vol. 30, iss. 2, pp. 97-108, 2016.
- A. Fakhari, M. Keshmiri, “Slippage Dynamic Modeling in Object Grasping and Manipulation with Soft Fingers,” Modares Mechanical Engineering, vol. 15, no. 8, pp. 332-340, 2015.
- A. Fakhari, M. Keshmiri, M. Keshmiri, “Dynamic Modeling and Slippage Analysis in Object Manipulation by Soft Fingers,” ASME International Mechanical Engineering Congress & Exposition (IMECE), Montreal, Quebec, Canada, Nov. 2014.
LinBot – Design, Analysis, and Field Test of a Novel Power Transmission Lines Inspection Robot
In this research, design, analysis, and field test of an innovative inspection robot (which is named LinBot) for highvoltage power transmission lines are investigated. This robot is utilized for moving on ground wires of transmission lines with the aim of inspection and fault detection of phase lines. Thanks to active and passive mechanisms designed in this robot, it is able to surmount all different ground wire obstacles including warning balls, clamps, and tower tips, and this is a unique capability of this robot among all other line inspection robots. The active mechanisms comprise four vertical rollers attached to the robot chassis by four arms, three horizontal rollers, and six mechanisms to control the vertical position of these horizontal rollers. Moreover, four sets of rotational springs and dampers are located in the joints of vertical rollers arms as passive mechanisms. To validate stability and feasibility of the robot in obstacle surmount and achieve the best selection for the robot required motors, a simulation study in MSC ADAMS software is conducted. The dynamical behavior of the robot including the motors torques is presented based on the simulation results. Furthermore, effect of wind on the stability of the robot is studied. Finally, practical performance of robot prototype manufactured in a laboratory is evaluated in the real field experimentally.
![]() | ![]() |

Publications:
- A. Fakhari and A. Mostashfi, “LinBot - Design, Analysis, and Field Test of a Novel Power Transmission Lines Inspection Robot,” 2019 7th International Conference on Robotics and Mechatronics (ICRoM), 2019, pp. 132-137, doi: 10.1109/ICRoM48714.2019.9071839.
- A. Mostashfi, A. Fakhari, and M.A. Badri, “Simulation and Experimental Validation of a New Cable Inspection Robot for High Voltage Lines,” Mechanical Engineering Sharif, vol. 31-3, no. 2, pp. 25-32, 2015.
- A. Mostashfi, A. Fakhari, and M.A. Badri, “A Novel Design of Inspection Robot for High-Voltage Power Lines,” Industrial Robot: An International Journal, vol. 41, no. 2, pages 166–175, 2014.
- A. Mostashfi, A. Fakhari, M. Sakkak, M. Sadeghi, and M.A. Badri, “Inspection Robot for High-Voltage Power Lines,” IR Registration No. 81449, Tehran, Iran, Dec. 18, 2013.
Trajectory Planning of Walking with Different Step Lengths of a Seven-Link Biped Robot:
Most of the essential parameters of human walking can be captured with a seven-link planar biped robot. In this project, dynamics modeling and trajectory planning of a seven-link planar biped robot walking on level ground with a ditch or stairs were studied. The hip and foot trajectories were designed in Cartesian space using polynomial interpolation such that to vanish the impact effect of feet with the ground. The key parameters of the hip joint trajectory in the x-axis direction were obtained using boundaries of biped stable region during the walking to satisfy the dynamic stability of the robot. The highest position of the swing foot ankle joint in the x- and z-axis direction was optimized with two different fitness functions. A novel method for trajectory planning of walking with different step lengths, uses for online trajectory planning, was proposed. Moreover, the effectiveness of the proposed method was verified by simulation and experimental results.

Publications:
- A. Fattah and A. Fakhari, “Trajectory Planning of Walking with Different Step Lengths of a Seven-Link Biped Robot,” ASME International Design Engineering Technical Conferences & Computers and Information in Engineering Conference (IDETC/CIE), Montreal, Quebec, Canada, Aug. 2010.
- A. Fattah, A. Fakhari, and S. Behbahani, “Dynamics Modeling and Trajectory Planning of a Seven-Link Planar Biped Robot,” 17th Annual (International) Conference on Mechanical Engineering (ISME), Tehran, Iran, May 2009.